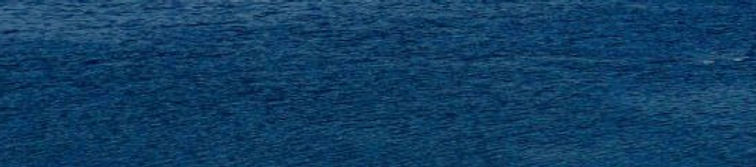
1331 E. St Gertrude Pl
Santa Ana, Ca 92705
714-486-1607
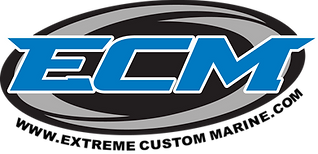
I
F
One of the most important components on your EFI engine is the fuel injector. The fuel injector sprays a precise amount of fuel into the intake manifold mixing with the incoming air from the throttle body. As the fuel sits in the injector for long periods of time, it will end up turning into a sticky varnish. When this happens the varnish will end up clogging the injector and prevent the injector from producing a nice even spray pattern. Typical symptoms of an injector that is partially clogged are; rough idle, hesitation, more fuel consumption (due to having to run more RPMs to accomplish the same speed), and more emissions.
Most of today’s injectors will have a filter in the injector to keep small debris from entering the injector and causing problems. There are fuel injection cleaner additives that can help keep the injectors clean. These additives usually work well in cars where they are driven every day and the fuel does not get a chance to evaporate. The additives are not the best choice for marine applications where the engine will not run in the winter for 6-9 months. To make sure you injectors are performing like new they should be removed from the manifold and flow on an injector flow bench. This way you can actually see the spray pattern as well as how much fluid they are able to flow. Once they have been ran on the bench, the injectors can then be ultrasonically cleaned. When using ultrasonic’s to clean the injector, it breaks down the harsh varnish on the inside of the injector. When the injector is very dirty, they may have to be cleaned more than once to restore the injector back to its original condition. Once the injector is clean, new filters are installed and reflowed to ensure they are producing the correct spray pattern and volume.
.FUEL INJECTOR SERVICING .

EXHAUST MANIFOLD TIPS
MARINE EXHAUST GENERAL:
When the time comes to replace your manifolds, the easiest way to insure getting the proper parts for the job is to take a look at your current exhaust system and write down the casting numbers which are on each part. In some cases the number is on the engine side of the manifold and may be hard to see prior to removal. Some manifolds may have no number at all, making it difficult, but not impossible to identify. This is where model number information is handy. Try and find your engine manufacturer and then match up to the model number information to that. In many instances your motor may be several years older than the boat. The mechanic or the boat owner, must be aware of the importance of proper gasket installation at the riser to manifold surface. Water leakage at this point is virtually always a gasket seal problem, not a defective part (however, water leakage at an improperly installed gasket will eventually damage the iron parts in addition to allowing water into the engine). Understanding the plumbing of a manifold may help in the installation and reassembly of your manifolds and risers. Familiarize yourself with the OEM service manual and make sketches or photographs of your plumbing system prior to disassembly. This may avoid problems with the installation. Remember to drain water from your manifolds and risers prior to removal of any of the pieces. Failure to drain the parts can result in damage to your engine due to water ingestion. Do not alter or modify gaskets. Order the correct parts for your installation.
MARINE EXHAUST PAINT:
Performance Product Technologies offers the industries only Ceramic Coated direct replacement marine exhaust system products. While other companies offer products with only primer or standard epoxy paint, PPT offers select products with corrosion resistant coatings and ALL of your required mounting hardware. The benefits of a ceramic coated product are that the coating will offer itself to corrosion before allowing any of the substrate material to degrade. There is no such thing as a totally corrosion resistant coating in that all coating are permeable to some degree and therefore will allow water to get behind the coating at some point down the road.
MARINE EXHAUST GASKETS:
The installer should remove all paint from the gasket surfaces before assembly of manifolds, risers, and elbows. Use acetone or lacquer thinner to remove the paint. Do not scratch, sand, file, or use high speed rotary gasket removers.
MARINE EXHAUST BOLTS & TORQUE:
Do not use stainless steel or grade 2 bolts to install the risers or elbows. These bolts are too soft and will not hold a torque setting, which can cause leaks at the gasket surface. Bolt torque should be reset after initial startup, while the engine is still warm. Refer to your original manufacturer's engine service manual for specific torque settings. As a rule of thumb we suggest about 40 Lb-Ft for 3/8 fasteners. HOWEVER THE MOST IMPORTANT THING TO REMEMBER WHEN TORQUEING MARINE EXHAUST PRODUCTS IS TO PERFORM IN A UNIFORM PATTERN IN ABOUT 2-3 SEPARATE SEQUENCES. 1) 10 LB-FT FOLLOWED BY GOING ON UP TO 25 LB-FT THEN FOLLOWED BY TAKING THE TORQUE UP TO THE FINAL RATING. THE TORQUE SHOULD THEN BE CHECKED AFTER RUNNING THE ENGINE FOR 30 MINUTES THEN AGAIN AFTER 20 HOURS. Never use anti-seize type products on bolts or studs as this can allow for loosening of the parts.
Studs: To prevent studs from backing out and causing leaks which can cause engine damage, use red thread locking compound. Follow the manufacturers recommendations for their installation and removal. Do not use anti-seize on bolts or studs as it is a lubricant and will cause fastener to back out.
MARINE EXHAUST PIPE PLUGS AND FITTINGS:
When installing pipe fittings or pipe plugs care must be taken to avoid over-tightening. Pipe plugs and fittings are tapered and an overly tight pipe plug or fitting can crack the casting. Do not use thread sealants which contain Teflon. Do not try to screw the plugs in flush with the casting, they only need to be snug.
MARINE CORROSION
Marine Corrosion is an electrochemical reaction that happens when electrons flow between metals that are connected or grounded through water. What does this matter to you? Marine corrosion is the defining factor with regards to the longevity of your boat engine, boat exhaust system and sterndrive. As it happens, this electrical action causes one of the two metals to literally be eaten away - marine corrosion. The process is greatly accelerated in salt, brackish waters, or in waters with a high mineral content.
For many people, marine corrosion is probably the one single largest factor in determining longevity to your boat engine, boat exhaust system, or sterndrive. It doesn't take a metallurgist to apply the many beneficial techniques one can use to protect their boat engine from marine corrosion, etc. With all of this in mind, the main thing to keep in mind is that you can beat the marine corrosion issue. How? Preventive maintenance! There are three basic things that will significantly increase the longevity of your boat engine, boat exhaust system, or sterndrive.
1. Fresh Water Cooling
2. Engine Fogging
3. Engine Protection Products
FRESH WATER COOLING VS. RAW WATER COOLING, OPEN COOLING VS. CLOSED COOLING
Investigate the various benefits of the closed type of cooling system. Relating to the Marine industry Closed Cooling refers to a cooling system that utilizes a closed/pressurized system containing a standard within the engine block and/or exhaust manifolds. These types of systems utilize some type of a a heat exchanger to remove the heat from the antifreeze. Most common are the standard tube in shell type heat exchanger. Another system is called a Keel Cooler and the typical Marine Heat Exchanger utilizes a bundle of copper tubes surrounded by a copper shell. Engine cooler units are very similar to and vary in size most commonly between 4" & 5". The terminology "# of passes" refers to the dividers in the raw water portion of the cooler and usually range between 3 & 6 in number. When looking at these "passes" when removing the end cap of the cooler and looking into the end they will appear as dividers similar to a pie being cut into pieces. This effect of this is that the water flow velocity is increased and therefore coolant efficiency is benefited. One common misconception is that increasing the coolant flow rate and velocity therefore does not allow the coolant time to properly remove the heat from the system. Regarding marine water pumps there are two different pumps of most concern; & . The circulating pump is very much like the pump on an automotive engine except with a bronze impeller, ceramic face seals and stainless steel backing plate. These pumps are typically bi-directional and fall into the category of "centrifugal pumps". The other pump family is a positive displacement pump meaning it actually produces lift capacity and can be thought of as the pump that supplies the raw water to the circulating pump in an open cooling system. In a closed cooling system this actually pumps the raw water through the raw water (tube) side of the heat exchanger. This raw water is then removing the heat from the anti freeze that the circulating pump is circulating through the engines and/or manifolds. Raw water pumps are typically belt driven, crankshaft driven, or in Mercruiser case with the Alpha sterndrive mounted inside the lower unit of the outdrive. One of the most common misunderstandings regarding pumps and heat exchangers is the thought that simply increasing the size of the heat exchanger will always increase the overall capacity of the system. The amount of raw water flow ultimately limits the efficiency of the system and therefore it is important to size the heat exchanger in conjunction with a pump that will provide an adequate flow rate to yield the proper operating temperature.
equate flow rate to yield the proper operating temperature.
RE-POWERING YOUR BOAT
It doesn't take long when looking at the price of new boats that one wants to start investigating the alternative option of replacing or repairing your existing marine engine.
Engine Rotation - No matter whether you choose a longblock or complete bobtail engine the rotation will be a very important factor to evaluate. Rotation with marine engines is always viewed from behind the engine looking towards the flywheel. Standard rotation (left hand) means the flywheel is turning counter clockwise looking at it from the rear, or another way to think of it is that the harmonic balancer will turn clockwise when standing in front of the engine looking at it. Opposite rotation engines (right hand) were common years ago however not regularly produced today as the later variety of transmissions; Hurth & Velvet Drive have negated the need for this as the gears can rotate either direction without issue.
Marine Engine Longblock - This term generally refers to the cylinder block heads as well as the required internals of the engine. Generally marine engine longblocks do not include the intake manifold, engine circulating pump, or flywheel. Depending on the brand product the "tin ware" (oil pan, valve covers, timing chain cover) may or may not be included. Much like the flywheel, since the tin ware is not considered a "wear" item some manufacturers do not include this with their marine engine longblock products.
Bobtail Marine Engine - This term generally refers to a complete new engine as required to complete a "drop-in" replacement project. Depending on the manufacturer of the product in question these products generally come complete with fuel, electrical, cooling, and exhaust systems as well as the engine mounts yielding it ready to drop right in when replacing a used up engine.
Common issues that arise when replacing a marine engine long block are whether the intake manifold will match, making sure the flywheel is correct, making certain the ignition system matches properly, and making the necessary adjustments for electric versus mechanical fuel pumps . With marine engine long blocks there are either remanufactured or brand new options however the prices are actually very close to the same for either option.
When it comes to the specific product your needs have to be evaluated since many design changes have taken place over the years including rear main seals changing, mechanical fuel pumps being eliminated, cylinder heads changing, etc.
Marine Engine Torque Vs. Marine Engine Horsepower
GENERAL
When it comes to engine horsepower versus engine torque in marine engine applications, most people make the common mistake of focusing on the marine engine horsepower rather than the marine engine torque. When it comes to both gas marine engines as well as marine diesel engines, in most cases focus should be directed to the torque more so than the horsepower. There is a common saying with in the OEM industry that "Horsepower sells a boat however Torque is what actually moves it". This could not be closer to the truth! One should realize that horsepower is really a measure of the torque over a given period of time. This taken into account by the rpm variable in the specification. The following equation may help to shed some light as well.
Torque = Hp x 5252 / Rpm (5252 is a constant)
It is interesting to note that the formula also verifies the typical torque bell curve when the torque trails off as rpm increases at the top end. One may consider that engines making torque at a lower rpm tend to work better in marine applications due to the fact that "most" boats tend to plane in the range of 2,000 - 3,000 rpm. It's not by chance that most marine engine manufacturers continue using the larger displacement - lower rpm, cast iron marine engines because of this fact. Many people wonder why these manufacturers haven't changed over to the high rpm engines the automotive industry has been converting to over the past 10 years; for the same reason the LT-5 Corvette engine and Lexus V8 engines didn't work very well in these marine applications --- nice Hp but at higher rpm's and therefore poorer low rpm torque characteristics.
Another interesting item to note is that since the proper method for propping a boat is to select the size prop that allows the engine to turn at it's maximum allowable rpm. It is required that a similar level of torque be produced at the top rpm condition as well as the proper planning rpm for a given boat hull (draw a straight line across the torque bell curve and see at what "lower rpm" this takes place. If this is not the case the selected prop will over-load the engine at the boats planning rpm and therefore yield very sluggish low rpm performance characteristics. For example a high revving engine that makes 400 hp at 5500 rpm would be making about 382 Lb-Ft torque (using the above formula) at 5500 rpm, since it would have a maximum torque output at probably 4,000 rpm it would be likely not to produce enough torque at 2500 rpm to make the boat plane very well since the prop was selected based on the 382 Lb-Ft value. Notice the higher the rpm an engine makes it's torque the worse this situation becomes.
In contrast to this; large engines that make significant horsepower at "very" low rpm's will therefore make a tremendous amount of torque, but at extremely low rpm. For example a diesel marine engine that makes 300 Hp at 2,000 is making 788 Lb-Ft at this same rpm. Noting that the torque curve is generated in "bell form", and therefore the maximum torque could be as high as 900 Lb-ft on this 300 Hp engine. Comparing this against a 300 Hp GM small V8 engine that makes 300 Hp at 5,000 and 375 Lb-Ft torque at 3200 rpm, this is a considerable difference. Very low rpm diesel engines typically make tremendous low rpm torque and therefore require specific gear ratios not supported by sterndrives, as well as requiring much larger diameter prop shaft's.
APPLICATION
Now realizing the above facts one may ask how this can be applied to my specific boat or especially gas to diesel conversion re-power projects. Since overall boat speed is generated by a combination of prop speed and prop pitch (the horizontal distance traveled by a single propeller revolution - measured in inches. Ex 21P means 21 inches of travel with one revolution). For most mid-size boats (up to 40 feet) the best option is a higher revving diesel engine that generates torque at lower rpm. For example a diesel engine that produces 300 Hp at 3600 rpm and makes 500 Lb-Ft torque at approximately 1600 rpm will work out much better than the example above of the 300 Hp engine making it's power at only 2000 rpm.
BOTTOM LINE
When looking to re-power or especially when looking to convert from gas to diesel, spend more time comparing the torque rather than horsepower. For example when converting from the typical 330 Hp GM 454 engine to a "high rpm" 300 Hp diesel, the additional 100 Lb-Ft torque produced by the diesel will allow approximately 5-6 more sizes in prop pitch and therefore offset the 1,000 rpm given up with the diesel. With the typical 250 Hp small V8 gas engine, a "high rpm" 250 Hp diesel will yield approximately 100 Lb-Ft additional torque and therefore match up very nicely.